Vire 7 electrical is very simple.
the ignition is self-powered and requires no external wiring.
a stop switch that shorts the points to the crankcase stops the engine/sparking
there is an AC generator output from the magnet, but it is generally useless/ignored unless you have no dynastart unit.
the charging/ starting is optional dynastart unit that is completely seperately wired
a connector block in front of the cylinder has four wires:
crankcase ground (bolted to crankcase, usually blue wire)
points/ contact breaker (for stopping engine, usually black)
AC output (for running small lighting loads, yellow pair)
I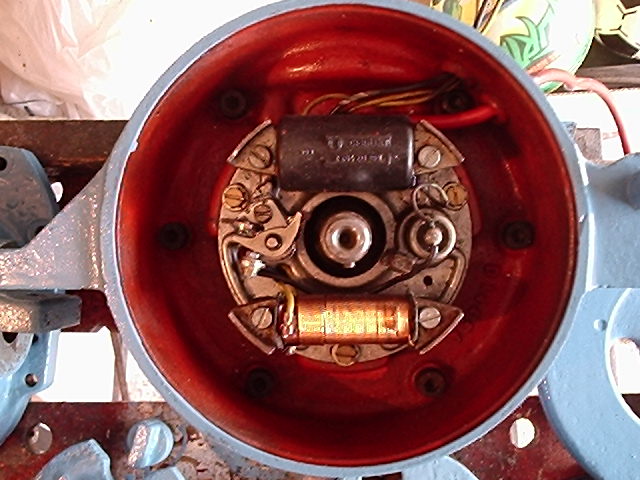
Ignition wiring
this is the best arrangement for controls:
single double pole double toggle switch from an electronics shop, and push to make button switch
with the switch up, the engine is off, one pole shorts points to ground, the other pole is open cct 12v to ignition lamp(dynastart regulator wiring)
with the switch down the engine can be run, the points short is open, the 12v to ign lamp closed.
press the button switch which sends 12v to the regulator units start terminal (starter solenoid)
have a choke cable set up near the push button, switch and lamp
also have throttle nearby, which can be mower/seagull throttle type to save space
gear control is contraversial, I have found them troublesome...
if they are connected to morse, 2 problems:
morse connections get loose and break leaving you stuck in gear
some morse does not allow revveing engine in neutral - essential with vire to clear oiling up plug if it is miss-firing before it stalls.
having the gearstick opearted directectly through a gap in the floof/step seems best but not always possible.
if you do use morse, dont fit rubbish.
dont bother with a rev counter, it's loud enough to be obvious if the engine is straining - basically having
tuned for max revs in gear using the carb t-bar, there is no point opening the throttle more if the revs dont increase.
in any case a tach is hard to find that works on one cyl magneto??
temp warning: I araldite a car radiator fan switch (about 88 deg C) onto the top of the cylinder, then wire a
12v piezo buzzer to earth and the switch. to the other switch terminal is wired your 12v ignition switch which also goes to the ign lamp.
This gives an audible warning if you forgot to open your seawater cooling valve before starting or any other
problem that causes overheating. the parts cost about £7, and it will gaurantee you dont seize the piston and ruin the cylinder which will be several hundred £.
DYNASTART / REGULATOR
The dynastart is a dynamo and starter combined, it does this by having a second set of field coils energised by the started solenoid which is inside the regulator unit.
the bosch units are quite powerful and although not as fast charging as an alternator, they will charge at about 11 amps or more which considering the 1 hour running per trip typical (motoring from the motoring
to the sea) is more than enough to top up a battery powering lights, instruments, laptops and of course starting too.
the dynastart unit is very expensive to buy and a working second hand unit is like hen's teeth' to find. but i have a few tested exchange units now.
When the charging on mine packed in years ago, I tried everything to get it working, stripped, new bearings, multimetered all windings, new brushes, cleaned commutator and grooves up, etc, eventually I
bought an entire engine for spares just to get it's dynastart. I now realise there is a common Bosch regulator fault that makes it look like the dynamo has packed in, which takes 10 secs to fix in situ and
means that my old unit probably was not faulty at all!
to test a dynastart, short DF to earth and disconnect D+. run up to medium revs, D+ should rise to above 14V. there should be approx 6 ohm reading between earth and disconnected D+ (i think it's those 2) or
the coils are blown.
if not, probably the coils are shorted/corroded/overheated due to its 'hot running' marine unventilated design. The field and starting coils are nearly impossible to remove from within the armature without a
special clamp, and it is easy to damage expensive coils and brushes and get it together wrongly connected unless you know what you are doing.
to check regulator, measure D+ over range of revs. when D+>battery voltage cut in relay should operate (top left), then as revs rise and D+ increases >13V right hand relay should start to lift off earth contact
(substituting resistor on rear instead of short to earth for DF), and as D+>13.8v right hand relay should pull fully shut (maximum resistance to DF).
The Bosch regulator has a removable cover (2 screws in sides). under the cover you see the two relays,
the starter solenoid to the left, the pull-in relay in the middle and the 3-position regulator on the right, just in
front of the regulator relay near the connection terminals to D- and D+ is a fusible link (20 amp fuse wire) soldered between 2 points - this should be intact. If there is a break of about 3mm it seems to been
deliberately snipped but in fact it has 'fused', you merely bridge with a blob of solder and it is FIXED!
what cause this to blow, is when the earth connection to the battery shakes loose, which means the regulated field which cannot instantly dissipate causes a massive overvoltage on the dynamo output
(running) and blows the protection fuse. In my case this year, I left harbour in a force 5, and the autopilot
and instruments suddenly dissapeared though the engine kept running. when i did stop the engine, i couldnt
start it as the earth had shaken loose (vire's are quite shaky), and even when I reattached the earth some
10 minutes later I noticed though the engine was starting again, there was no charging and the instruments were not all restored (the voltage had blown the Stowe wind inst fuse first).
How the regulator works: April 2006 update:
as the Dynamo output rises a volt or so above the battery voltage - the cut-in relay connects it to the battery. -
this will cut out as it falls below battery voltage (to prevent hysterisis). As the engine speeds up, the dynamo
output (with no field resistance) rises above 13.5V, then to prevent boiling of the battery, the regulator relay is
pulled off the zero resistance pole and substitutes a small resistance in the field (DF) circuit, further raising
dynamo RPM causes this regulator to pull to the other pole which substitutes a larger resistance in circuit, thus reducing dynamo output.
problems: - invariably the pole contacts are blackened or corroded - a cheaper alternative is the Lucas 4ATR unit? but this requires seperate solnoid for starting.contact may be cleaned with emery paper and WD40, but
ensure battery disconnected before you do. ideally fold 10mm strip of wet&dry paper double-sided (now
5mm), then slip between contact pairs, as you draw out your long(>30mm) strip, press the contacts together with
insulated stick/finger, then having removed strip with contacts opened, blow out dust, and flick the contacts apart so they snap together - crushing/ejecting any dust between.
WD40 the outside of the control regulator every year, and dont ever allow seawater to ingress/drip onto it.
Checking charging.
Voltmeter on battery must increase when engine is running, between 13V and 14.0V between fast idle and full throttle RPMs.
We got home safely, although I had to sail to guess the wind a lot more.
WIRING, refer to owners manual http://gofree.indigo.ie/~vire7/electric.htm
but basically it is as follows:
Bosch Regulator :
31= Earth / case of regulator / batter / dynamo chassis via bolt in it's body
30h=switched 12v solenoid output to starter coils
30B+=12V input from batter, also connected to ignition switch
DF=dynamo field connection - when this is earthed it allows unrestricted D+ output - the regulator adds resistance/open cct to earth as D+ rises above 13/13.8V
61D+=dynamo output, also connected to ign lamp negative side (static 0v lights lamp but rises to 13v when running and extinguishes 12 V lamp)
the vire pack includes a 3 position switch that allows you to switch over to AC lighting while running -
pathetic, not only does it make a key neccesary to use (or lose), but it interupts the DC out while starting -
thus when your engine cuts out and you turn the key against it's spring to restart, it knocks out all your nav
equipment, autopilot and such. in an instant you lost your GPS fix, the depth profile and your autopilot.
See above for my solution earlier on this page.
in 1963 when these things were being distributed new, they hadnt thought of GPS and autiopilots being on most small cruisers.
I suppose in those days, an engine was considered a luxury anyway as you were supposed to sail or tow your cruiser by towing it with a rowed tender!
|